طراحی و ساخت انواع پرینترهای سه بعدی فلزی و پلیمری و توسعه زیر ساختهای آن
محور پژوهش
ماشین آلات و تجهیزات پیشرفته
پژوهشکده/دانشکده
مهندسی مکانیک
حوزه پژوهش
تجهیزات ساخت و تولید مواد و قطعات فلزی، سرامیکی، پلیمری و كامپوزیتی
عنوان
طراحی و ساخت انواع پرینترهای سه بعدی فلزی و پلیمری و توسعه زیر ساختهای آن هدف از اجرای پژوهش، کاربردها، مزیتها و ضرورت انجام پروژه: در سالهای اخیر عوامل متعددی نگرش و نحوه زندگی افراد بشری را دستخوش تغییر نموده اند. از یک طرف روند افزایش جمعیت کره زمین ومتعاقب آن افزایش تعداد جویای کار و درآمد، رقابت سختی را بین شرکت های صنعتی وخدماتی جهت کارآقرینی، بقا یا حفظ سهم بازار وافزایش سوددهی موجب شده است. از طرف دیگرارتقای سطح درآمد افراد منجر به بروز نیازهای متنوع و جدیدی شده است. بعنوان مثال امروزه محصولات و خدماتی اختصاصی(customized) ، آماده بهره برداری در کوتاهترین زمان ممکن، با کیفیت و کارایی سطح بالا، و مقرون به صرفه از لحاظ اقتصادی مورد درخواست هستند. محدودیت منابع طبیعی کره زمین و لزوم تلاش در جهت حفظ محیط زیست از جنبه های دیگر ملاحظات امروزی می باشند. ایجاد، گسترش و بکارگیری فناوری های پیشرفته در طراحی، تولید و خدمات تلاش بشر جهت پاسخ به نیازها وچالش های اشاره شده می باشد. فناوری های ساخت افزودنی (Additive Manufacturing_AM) از جمله این فناوری ها می باشند که حتی به عنوان انقلاب صنعتی سوم نام برده شده اند. ساخت افزودنی که به نام چاپ (پرینت) سه بعدی(3D Printing) نیزشناخته می شود، طبق استاندارد ASTM F42 فرآیند اتصال مواد خام برای ایجاد قطعات از اطلاعات مدل سه بعدی (3D)، معمولا بصورت لایه-لایه وبر خلاف روشهای براده برداری تعریف شده است. اگرچه روشهای AM ابتدا با عرضه مواد فوتوپلیمری وسپس پلیمری در دهه1980 و عمدتا جهت نمونه سازی سریع معرفی شدند، ولی پیشرفتهای بعدی نه تنها منجر به گسترش دامنه مواد قابل فرآوری و ظهور روش های جدیدتری شده اند، بلکه تولید قطعات کاربردی با خواص مکانیکی و متالورژیکی عالی را امکانپذیرکرده است. از آنجایی که روش های AM با اضافه کردن تدریجی ماده در هر جا که لازم باشد قطعه را می سازد، امکان ساخت قطعات بسیار پیچیده ای را فراهم می سازد که معمولا بوسیله روش های مرسوم تولید، قابل ساخت نمی باشد. تکنیک های AM نه تنها منجر به کاهش هزینه ها و زمان ساخت قطعات تولیدی شده اند، بلکه این امکان را به وجود آورده اند که قطعاتی که با روش های معمول قابلیت تولید ندارند، قابل ساخت باشند. در کنار کاربردهای معمول بسیار گسترده تکنولوژی در فرآیند طراحی محصول و ساخت قطعات نمونه، صنعتی، پزشکی، دانشگاهی و تحقیقی، حوزه های صنعتی پیشرفته نظیرصنایع هوافضایی، تولیدانرژی، و اتومبیل سازی فرآیند پرینت سه بعدی را بعنوان یک روش جدید تولید به کار گرفته اند. با توجه به نیاز ضروری کشور به این تکنولوژی ها از سال 1391آزمایشگاه ساخت افزودنی دانشکده مهندسی مکانیک تاسیس گردیده و با همکاری شرکت های دانش بنیان اقدام به طراحی، ساخت، و نصب پیشرفته ترین سیستم های پرینت سه بعدی شامل فناوری های ذوب گزینشی بوسیله لیزر (selective laser melting_SLM)، تف جوشی گزینشی بوسیله لیزر (selective laser sintering_SLS)، ورسوب مستقیم فلز (direct metal deposition_DMD) یا laser cladding نموده است. گزارش و شرح زیرساختها، فعالیتها، و دستاوردها فناوری SLM که دانش طراحی و ساخت آن در انحصار تعداد معدودی از کشورهای توسعه یافته می باشد، توسط شرکت دانش بنیان مستقردر شهرک علمی تحقیقاتی اصفهان و با همکاری اعضای هیات علمی دانشکده طی سه سال به بهره برداری رسیده است. این سیستم ها قادر به فرآوری انواع پودرهای فلزی بوده و قطعاتی را با خواص مکانیکی و متالورژیکی عالی تولید نماید.خواص مطلوب قطعات تولید شده گواهی تاییدیه کیفیت را از آزمایشگاههای مرجع و صنایع استفاده کننده دریافت نموده است. تاکنون چندین نسل از دستگاهها با اندازه های مختلف تولید و تجاری سازی شده اند. این محصولات دانش بنیان هم اکنون در تعدادی از مراکز تحقیقاتی، دانشگاهی و صنعتی کشور در حال بهره برداری می باشند. بعنوان مثال شرکت مهندسی و ساخت توربین مپنا_توگا هم اکنون دو دستگاه از این سیستم تولیدی را در کارخانه خود نصب نموده و مشغول بهره برداری می باشد. انتظار می رود با ایجاد زیرساخت های این تکنولوژی در کشور در آینده ای نزدیک از قابلیت های این فناوری ها در کشور استفاده کافی برده شود. آزمایشگاه ساخت افزودنی دانشکده مکانیک مجهز به نسل اول این سیستم NOURA M100 می باشد. سیستم تف جوشی لیزری(SLS) قادر به فرآوری انواع پلیمرهای ترموپلاستیک به روش مستقیم و مواد سرامیکی به روش غیرمستقیم می باشد. این سیستم مجهز به یک لیزر پیوسته گازی دی اکسید کربن بوده وفضای ساخت آن استوانه ای به قطر 100 میلیمتر و ارتفاع 120 میلیمتر می باشد. سیستم مجهز به گرمک های مقاومتی و تشعشی بوده که قادر است دمای بسترپودر را تا 180 درجه سانتیگراد گرم نماید. طراحی سیستم گرمکن ها و کنترل دقیق دمای سطح پودر توسط سنسورهای غیرتماسی تعبیه شده امکان ایجاد دمای یکنواخت در سطح بستر پودر را فراهم می سازد. امکان طراحی و ساخت انواع ایمپلنت پلیمری و یا سازه های داربستی، در کنار تولید قطعات پیچیده از جنس پلیمرهای مهندسی از دستاوردهای این تکنولوژی می باشد. سیستم لیزر کلدینگ یا DMD طراحی شده مجهز به یک دستگاه لیزر پیوسته حالت جامد با توان 400 وات و یک میز CNC سه درجه آزادی، سیستم انتقال و پاشش دقیق پودر، و سیستم اپتیکی لیزر می باشد. این سیستم جهت تعمیر قطعات حساس نظیر قالبها و پره های توربین مناسب می باشد، ضمن اینکه امکان ساخت قطعات سه بعدی از فلزات مختلف را امکانپذیر می شازد. طراحی و ساخت این سیستم آزمایشگاهی و پروژه های تحقیقی انجام شده یا در دست انجام در این حوزه در دانشکده، دانش فنی بسیارموردنیاز صنایع تولید انرژی و نفت و گاز کشور را ایجاد کرده است. نسل اول پرینتر سه بعدی فلزی NOURA M100
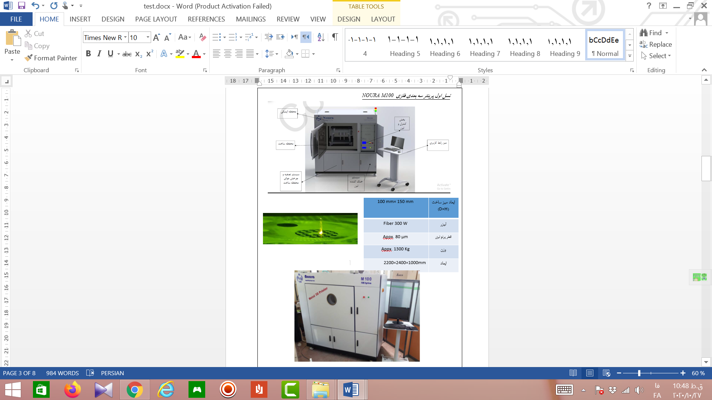
نسل دوم سیستم SLM: NOURA M100P
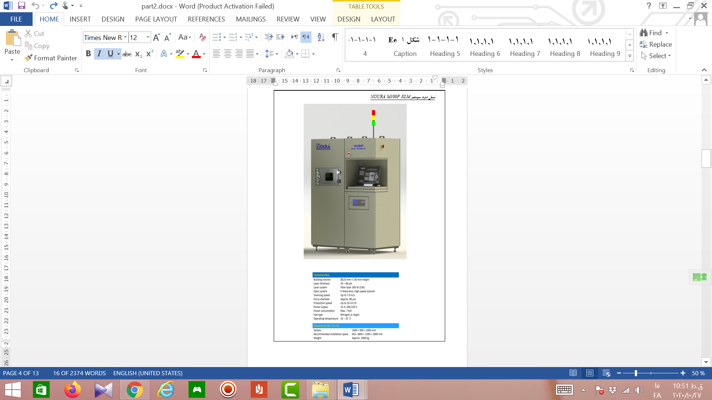
سیستم تف جوشی لیزری (SLS):
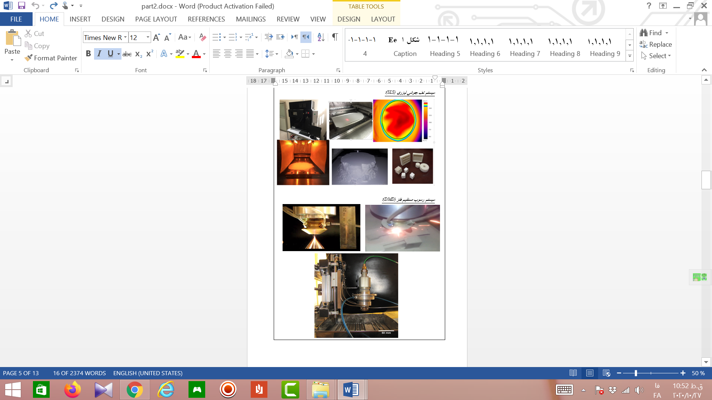
سیستم رسوب مستقیم فلز (DMD):